-
Chengli Automobile Industry Park
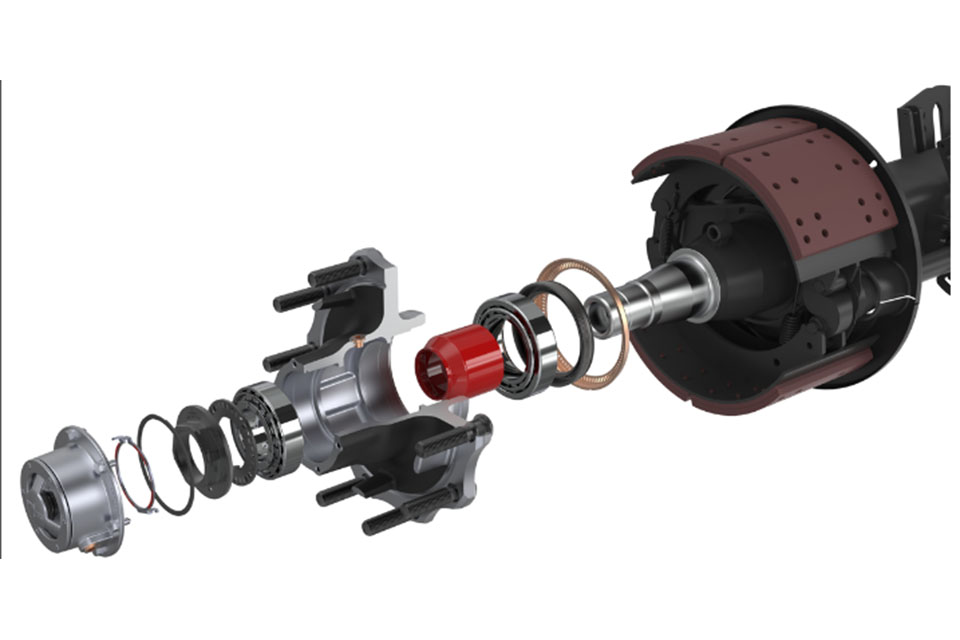
Discussion on maintenance-free products and related technologies for semi-trailer axles
Maintenance-Free Semi-Trailer Axle Technology: Cutting TCO and Boosting Safety
When you own a semi-trailer, the costs add up fast. Fuel, tolls, and wages are just the start. What many owners don’t see coming are the hidden costs of axle maintenance. Maintenance-free axle systems can solve this problem, helping trucks stay on the road longer while costing less over time.
Table of Contents
Why Maintenance-Free Axles Matter
Regular semi-trailer axles need lots of care. You must:
- Check wheel bearings often
- Replace lubricants
- Inspect brake parts
- Take wheels off for checks (“wheel removal”)
This all costs time and money. When trucks sit in shops, they don’t make money.
With maintenance-free axles, you get:
- Lower total ownership costs (TCO)
- Better safety records
- Higher truck availability
- Fewer roadside breakdowns
How Maintenance-Free Axles Work
The key to maintenance-free axles is bearing life. Bearings work best when they have the right amount of space (called “clearance” or “endplay”). This space should be between -0.025mm and +0.152mm.
When bearings have this perfect space, they last much longer. There are three main ways to get this right:
1. High-Precision Axle Nuts
This method uses special nuts that can set the bearing space very precisely.
Popular products include:
Product | Company | Precision | Maintenance Cycle |
---|---|---|---|
Zip-Torque | Stemco (USA) | 0.001″ | Needs manual checking |
Precision 320 | Hendrickson (USA) | 0.00026″ | 7 years/110,000 km |
800K Hub | BPW (Germany) | 0-15° rotation | 3 years/80,000 km |
The Hendrickson system stands out because it uses an outside brake drum design. This means you can fix brakes without taking the wheels off – a huge benefit!
Semi-Trailer Axles: Maintenance-Free Benefits
Discover how modern axle technology saves money, extends lifespan, and improves safety.
Lower Total Cost (TCO)
Up to 30%+ Savings
Reduced maintenance, fewer breakdowns, less downtime.
Extended Lifespan
3-7+ Years
Longer component life with optimized lubrication and sealing.
Improved Safety
Reduced Failures
Consistent performance, fewer bearing issues, better reliability.
Lubrication Matters: Oil vs. Grease
Theoretical bearing fatigue life under ideal conditions (13t axle load, 95 km/h equivalent).
Warranty & Maintenance Periods (Examples)
*Kilometers shown represent typical warranty periods, actual lifespan may vary.
How Maintenance-Free is Achieved
Precision Nuts
Uses highly accurate nuts for initial bearing setup. May still need checks. (e.g., Stemco, Hendrickson)
Bearing Units
Pre-assembled units with set clearance. Higher replacement cost if fails. (e.g., SKF, Timken)
Set-Right System
Precisely matched components (hub, bearings, spacer) for automatic clearance. Most robust. (e.g., Conmet)
2. Pre-Set Bearing Units
These come with the perfect bearing space already set at the factory.
Examples include:
- SKF THU2 (Sweden)
- Timken UniPac (USA)
- FAG THU (Germany)
These units come pre-sealed and pre-greased. They offer 3 years or 50,000 km of maintenance-free operation.
While simple to install, they have downsides:
- High replacement costs
- Can’t mix-and-match parts
- Need special tools for installation
- Might fail sooner on rough roads
3. The Set-Right System Approach
This is the most complete solution. It uses all matched parts that work together perfectly.
Key products include:
Product | Company | Features | Maintenance Period | Key Benefit |
---|---|---|---|---|
Preset | Conmet (USA) | Oil lubrication, sight window | 3 years/50,000 km | Works in extreme temps |
Preset Plus | Conmet (USA) | Advanced sealing | 5 years/80,000 km | Lower TCO |
800K | BPW (Germany) | Maze sealing, separate lube spaces | 3 years/80,000 km | Great for rough roads |
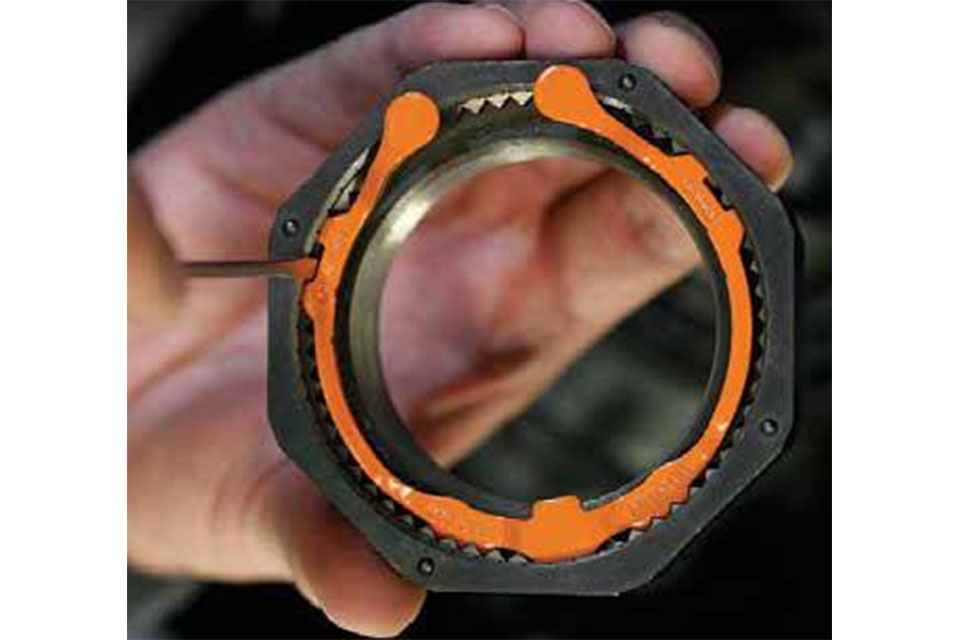
Oil vs. Grease: The Big Difference
One major finding: oil lubrication lasts much longer than grease. Testing shows:
- Grease lubrication: 52,300 hours (about 5 million km)
- Oil lubrication: 191,000 hours (about 18 million km)
That’s 3.6 times longer life with oil! The Conmet system uses this to great effect, with a clear window to check oil condition.
Choosing the Right Technology
Pick your system based on your needs:
- For extreme temperatures: Conmet Preset with oil lubrication
- For rough roads: BPW 800K with maze sealing
- For cost-conscious fleets: Hendrickson with outside brake drums
- For standard operations: Any maintenance-free system beats traditional axles
The Outside Drum Advantage
Tractor units for semi-trailers paired with outside brake drum designs have a big edge. With traditional “inside” drums, you must remove the hub to fix brakes. Outside drums mean:
- Brake service without wheel removal
- Hub system stays sealed
- No dirt gets into bearings
- Longer bearing life
What Users Are Saying
Fleet operators using maintenance-free systems report:
- 30% lower maintenance costs
- Fewer roadside breakdowns
- Better uptime and truck availability
- Reduced risk of catastrophic failures
Which System Is Best?
The Set-Right approach (like Conmet Preset) offers the most benefits:
- Parts work together as a system
- No manual adjustments needed
- Oil lubrication for longest life
- Visual inspection without removal
- Works in all climates
For heavy-duty hauling, the BPW 800K system handles the toughest conditions with its maze sealing design.
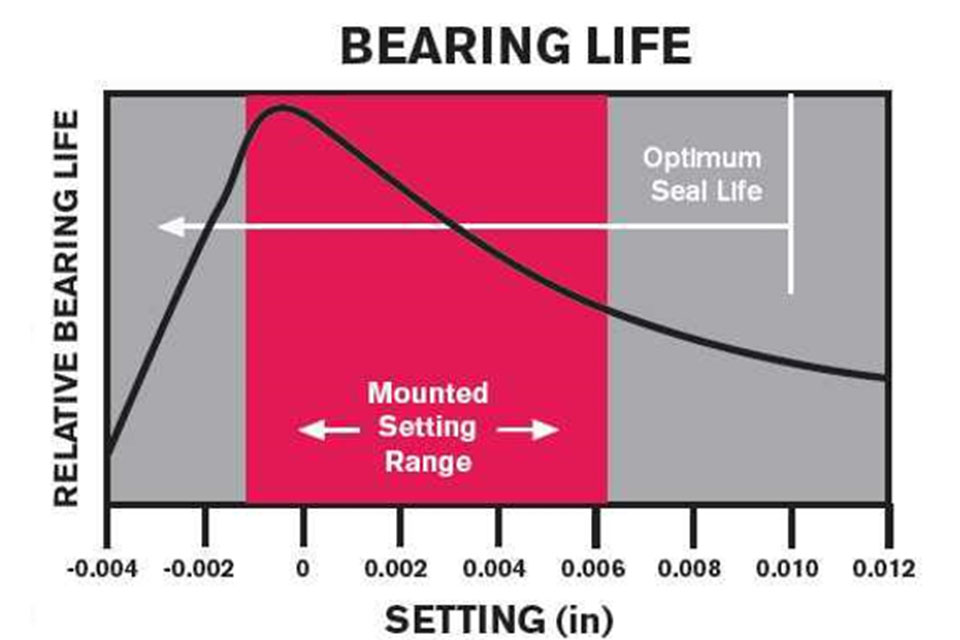
Conclusion
Maintenance-free axle technology isn’t just nice to have – it’s a smart business move. By picking the right system, semi-trailer owners can:
- Cut total costs significantly
- Improve safety
- Keep trucks on the road longer
- Avoid surprise breakdowns
The best systems combine oil lubrication, outside brake drums, and precision manufacturing. While the upfront cost may be higher, the savings over time make maintenance-free axles well worth the investment.
When buying your next semi-trailer, consider these technologies – your bottom line will thank you!