-
Chengli Automobile Industry Park

Analysis of magnetic pulse welding process for aluminum-steel metal panels of automobile bodies
Imagine building a car that’s strong yet lightweight, like a hummingbird’s skeleton. Modern cars use aluminum and steel mix together, but welding them is tricky. This is where magnetic pulse welding steps in—like a superhero tool for automotive engineers!
Table of Contents
How It Works: Faster Than a Speeding Bullet
The Power Behind the Punch
Magnetic pulse welding shoots one piece (the “flying plate”) at the other (the “base plate”) at 350 meters per second—three times faster than a speeding bullet! This isn’t magic—it’s science:
- Electric Booms:
A giant capacitor zaps energy into a coil, creating a microsecond magnetic explosion. - Launchpad Magic:
The flying plate (usually aluminum) gets pushed by this magnetic wave. - Collision Magic:
When the two metal pieces collide, they fuse like two drops of water merging.
Key Insight | Why It Matters |
---|---|
No Heat = No Weak Spots | Unlike old welding torches, no melting means stronger joints. |
Clean & Green | Zero fumes or sparks make workshops safer for you and the planet. |
Tuning the Welding Machine: The Secret Sauce
Dialing In the Perfect Shot
Think of this like adjusting a high-tech dartboard. Three controls matter most:
- Energy Boost:
More electric juice = faster flying plate. Too much could crack the weld. - Spacing Matters:
0.6-1.8mm gap = sweet spot. Perfect for aluminum and steel’s love-hate relationship with heat. - Material Match:
Aluminum’s high conductivity + steel’s magnetic pull = perfect partners for this tech.
Choosing the Perfect Setup: Real-World Testing
Gap (mm) | Speed (m/s) | Best Use Case |
---|---|---|
0.6 | 260 | Lightweight parts (car doors) |
1.0 | 350 | Standard panels (hoods) |
1.8 | 450 | Heavy-duty sections (frame rails) |
When gaps shrink, speed drops fast—like slamming on brakes at a red light.
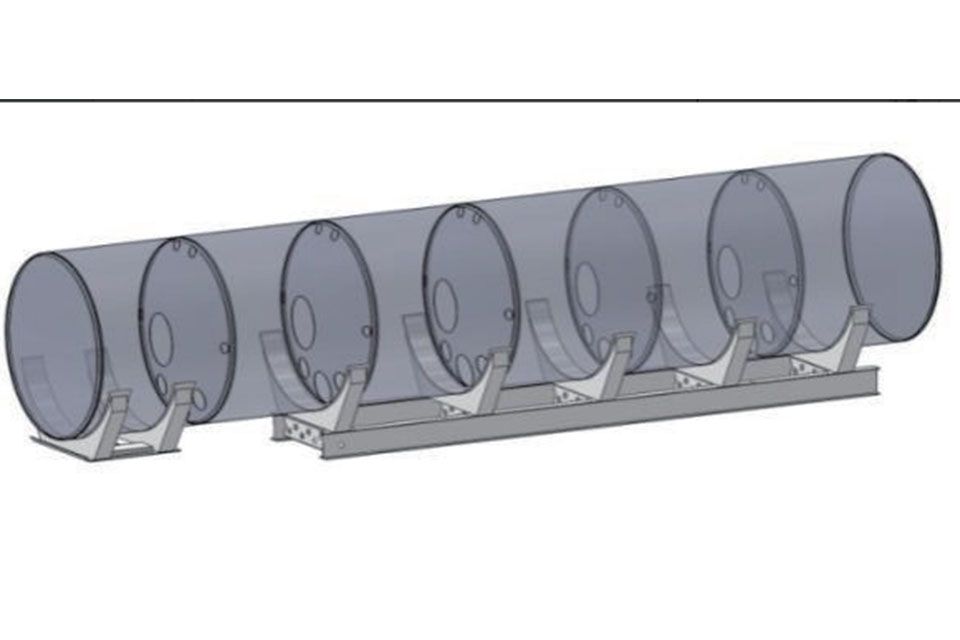
Real-World Superheroes: Where the Magic Happens
Making Cars of the Future
This tech isn’t just for regular cars—it’s a game-changer for specialist vehicles:
- Electric Cargo Trucks:
Lightweight aluminum bodies on mean longer battery life. - Emergency Vehicles:
Fire trucks (like this rescue model) get stronger panels without adding weight. - Construction Giants:
Attachments for concrete pump trucks can mix materials without rust worries.
PRO TIP: Interested in eco-friendly transport? Check out zero-emission electric trucks using this tech!
Why This Matters: A Lighter Future
The Big Picture
Auto engineers once said “Lightweight + Durable = Impossible”—until磁 pulse welding came along. Here’s the payoff:
- Safer Cars: Hybrid metal structures absorb crashes better.
- Cheaper Transport: Less weight = less fuel or battery drain.
- Greener Planet: Fewer emissions from lighter trucks hauling goods.
The Future Is Pulse-Driven
From your daily commute to massive construction projects, this technology is here to stay. The next time you spot a shiny car body, remember: magnetic marvels are at work behind the scenes!